DIGITALIZATION:THE NEW SCIENCE OF WINNING
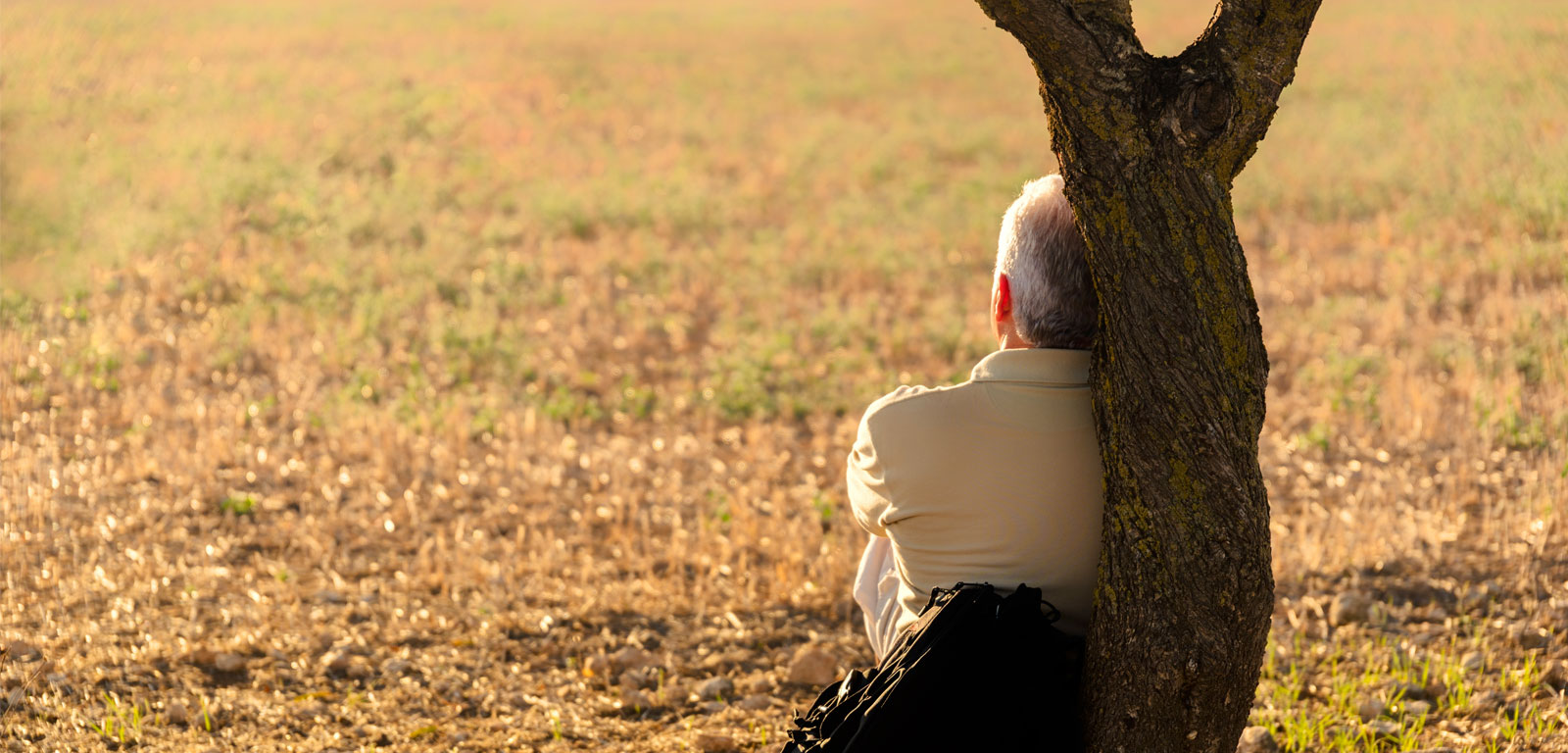
Those who have not yet begun the transition are realizing that digital transformation is a no-regret move: it brings huge benefits to machine producers, manufacturers and final consumers.
DIGITAL MACHINERY: TRENDS AND NUMBERS
Selling equipment and components is no longer enough: machine producers are now embracing digitalization and Industry 4.0 because providing integrated solutions and digitalized equipment to their customers has resulted in market differentiation and increased market share. According to FutureBridge, machine manufacturers across the globe will invest more than US $100 billion in the next three years on digitization with 20% of companies expected to invest more than 10% of their annual revenues.
WHO SHOULD LEAD THE DIGITALIZATION PROCESS?
At the same time, it’s not just machine producers who are betting on Industry 4.0: digitalized solutions are an advantage especially for their customers, manufacturing companies, who can extract useful information with IoT and AI and use it to operate equipment at peak efficiency and productivity.
That’s why companies are prioritizing digital efforts in every sector as a way to create greater business value. However, according to a Harvard Business Review Analytic Services survey this is only the beginning because:
“Of 727 executives worldwide, 92 percent say their organization’s digital transformation will become more important to business success in the next 12 months”.
On a more practical level, another FutureBridge analysis shows that more and more companies are choosing to go for artificial intelligence-capable machinery: if in 2019 the number of digital machineries was around 1.5 million, by 2024 it is expected to reach 16 million units, growing at a CAGR of 60%.
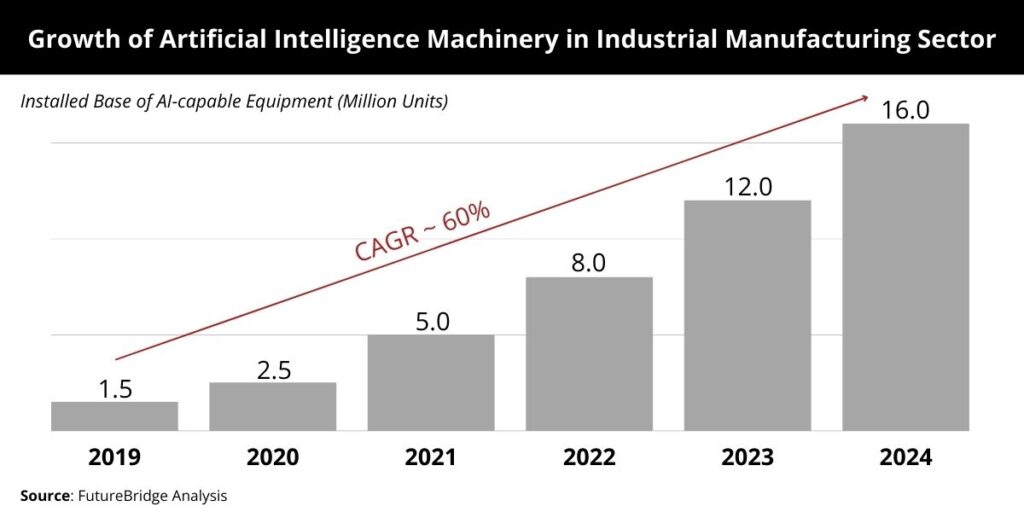
Although digitalization did not truly begin until 2021, the outcomes are already showing: in a recent McKinsey study, 50% of surveyed companies, after adopting digital strategies, reported moderate to significant impact on realizing new revenue streams, almost 70% reported impact on increasing existing revenue streams, and 76% reported impact on reducing costs.
DIGITALIZATION & ENTREPRENEUR’S PEACE OF MIND
Digitalization helps businessmen make better and faster operational decisions based on predictions and classifications learned from large dataset. This has a direct impact on process flows and in turn, it enhances efficiency by producing better outcomes.
At the same time by adopting a digitalized environment, decision makers will have access to comprehensive data from anywhere, which allows them to obtain better insights from analytics and always have full control over the business as a whole. But it’s not just about gathering data: thanks to machine learning, this enormous amount of information can be processed by AI and used to assist entrepreneurs in many tasks, such as supply chain management, product design or even for predictive maintenance.
Summing up, here’s what to expect from integrating Industry 4.0 in manufacturing plants:
- Product and process improvement;
- Quality tracking
- Stronger bottom-line
- Increase in plant productivity
- Faster decision making
WHERE DOES THE HOME TEXTILE INDUSTRY STAND?
PROCESSES: Like every other industry, home textile has been influenced by IoT, AI and digitalization as a whole. The industry is transforming right under our nose, with many steps already taken such as the high degree of automation over the complete textile fabrication process, but the transition between Industry 3.0 (the computer powered industry) and Industry 4.0 (smart factories) is still ongoing.
For the future, there will be no other option but to choose to go digital for textile companies and to do so it’s necessary to rethink the process and how things are done: from custom reporting and analytics on any chosen parameter (weight accuracy, target tracking, transport savings…) to automated cycle counts; from optimizing blends digitally to detecting fiber and product characteristic using AI, these are elements companies will need to use to increase efficiency and production and remain relevant in the market.
Process changes and continuous improvement both interact each other and one is dependent from the other: they need to be aligned!
PRODUCTS: The other side of digitalization is product optimization, that is adding digital capabilities to physical products. One of the first examples of that in the bedding sector was mattresses and cushions with sensors that were able to monitor sleep and provide reports. Building on this concept, Xsensor Technology Corp. recently presented a software which helps buyers choose their mattress: after lying down on it, a map with pressure points is created and buyers know which bed is more suited to redistribute the pressure more equally.
Overall, product digitalization allows buyers to interact with products and obtain information in digital format: the company Triple R, for example, provides information about their products through a RFID, embedded in the mattresses: buyers are able to follow the life cycle of the items or simply track it for logistics. These are all useful information made available at any given moment not only to consumers, but also to manufacturers and suppliers, who can use the data for product improvement and, in particular, to enable better quality and safety control.
IS THIS PROCESS STRATEGIC TO MY BUSINESS?
This is what a lot of companies are wondering and the short answer is: Yes, digitalization is a strategic choice for any business. Many people think that to start the transition it is necessary to have powerful (and expensive) tools such as high-performance servers, unlimited clouds and so on. Actually, this is not the case: digitalization is flexible and can be tailor-made to the company, it is not the other way around.
Here’s what a simple digital infrastructure in the bedding, upholstery and foam production sector can look like:
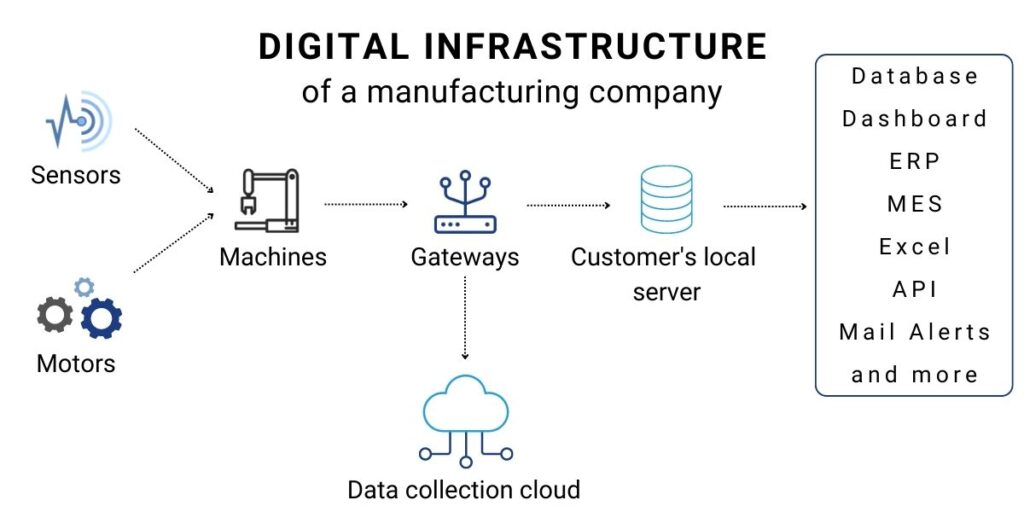
Although accessible to everybody, to implement a successful digital strategy it is imperative to carefully plan it. Here’s what you can do today to start the process:
- Set clear goals and expectations: what are your expected strategic outcomes?
- Analyze current resources: how can these new digital tools be incorporated in what you already have?
- Create a strategy: which solutions align with your long-term goals and available resources?
Considering the urgency to digitalize machines and plants and the strategic investments manufacturers will face, it is imperative that they find the right partner to study together goals and needs in order to identify exactly which digital tools can be most useful to take advantage of the automation, scale, and flexibility that this transformation offers.
HOW BRIGHI IS HELPING COMPANIES
“It is remote assistance and predictive management” says Riccardo Gardelli, Senior Digital Manager, in charge of Brighi Digital Division, “that’s what we are betting on. Remote assistance is our way to make the relation between our customers and technical team more efficient and make assistance cost-effective: that’s why we’ve integrated it in all our equipment. With that, we can identify and analyze the data at any time to reveal anomalies and provide support without having to actually be present, thus reducing machine downtime. The results are astonishing: we are able to solve 95% of issues remotely.
Predictive management on the other hand is the core concept behind our software Callisto – starting from the data collected from sensors, it constantly monitors and analyzes equipment conditions and makes predictions about its operation. It is particularly useful for predictive maintenance because the software alerts you before an issue occurs and informs you on when to carry out interventions at the most appropriate time.
Our digital division works closely with our customized project development team; together we are able to combine automation and process improvement – including high-level design, detailed process flows, measurement of before and after costs and cycle times. So that our customers can get the most out of digitalization!”
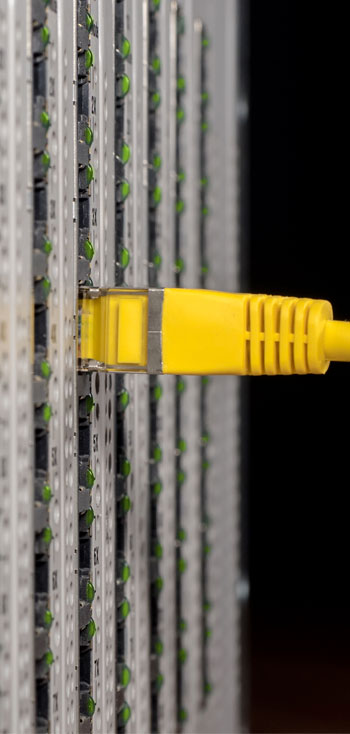