SOLUTIONS TO ENHANCE
YOUR HOME TEXTILE PRODUCTION
DAL 1970, MACCHINE AUTOMATICHE E LINEE COMPLETE PER IL SETTORE DEL BEDDING, DEL MOBILE IMBOTTITO E PER LA PRODUZIONE DI POLIURETANO ESPANSO
Dalle macchine modulari, implementabili passo dopo passo con un semplice Plug & Play, alle linee complete. I nostri sistemi automatizzati rispondono alle molteplici esigenze dei produttori di guanciali, cuscini decorativi e da esterno, cuscini multicamera per divani e poltrone, cucce per animali e oggetti imbottiti, trapunte e piumoni, blocchi di poliuretano per materassi, per soddisfare sia chi cerca tecnologie avanzate per una specifica fase di processo sia chi cerca soluzioni integrate, sempre all’avanguardia.
MACCHINE
Macchine per la produzione di cuscini, guanciali, trapunte, divani, cucce per animali, peluche e molto altro ancora
Linee Complete
Un unico fornitore per l’automazione del processo, dalla lavorazione della materia prima, fino al confezionamento del prodotto finito
Prodotti
Foam
Cuscini e guanciali soffiati
Cuscini e guanciali cardati in fibra arrotolata
Cuscini in lattice e gommapiuma
Tappeti
Trapunte
Cuscini per divani
Production waste
LE PROSSIME FIERE
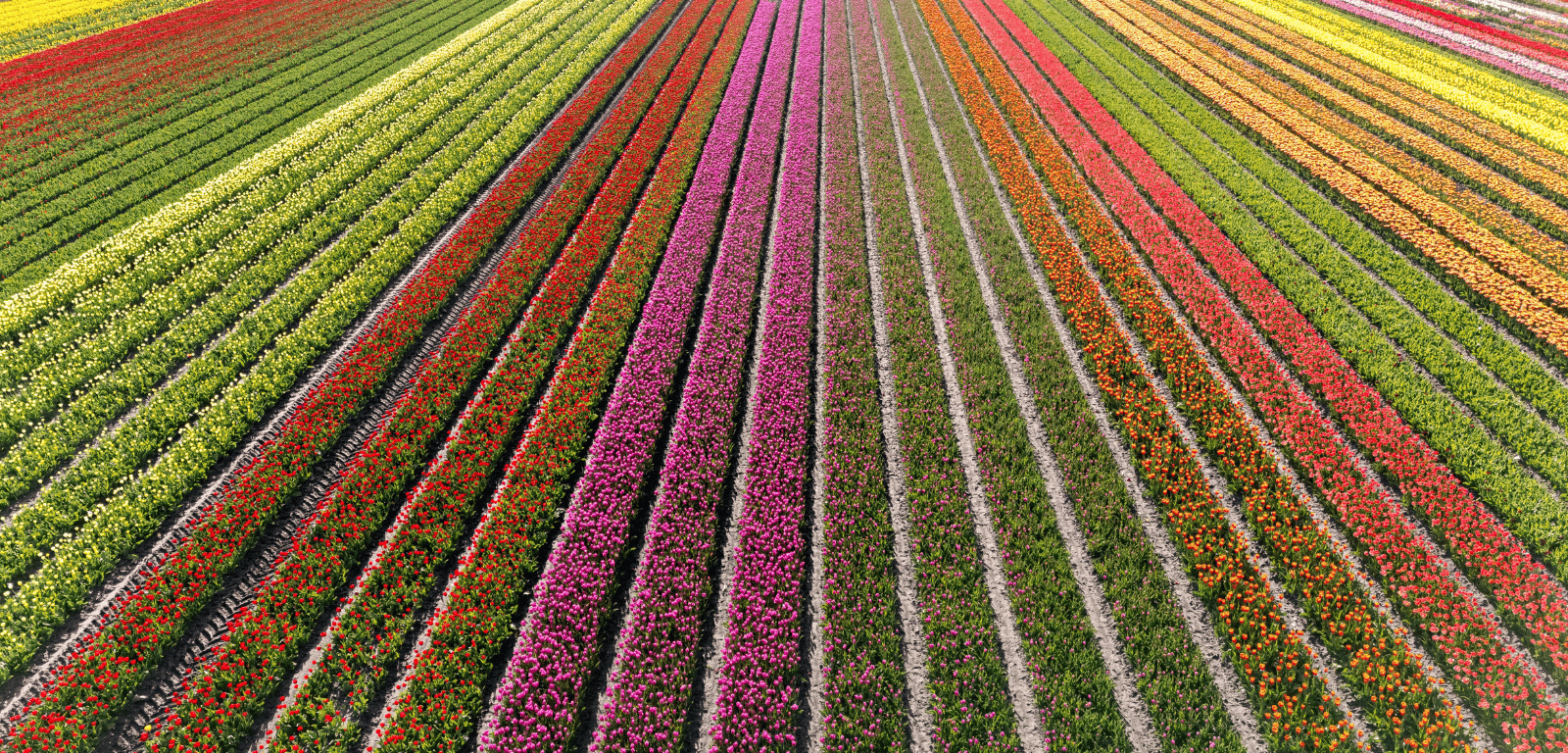
AUTOMATIZZAZIONE E PACKAGING: UNA NUOVA ERA PER L’INDUSTRIA DEI TAPPETI
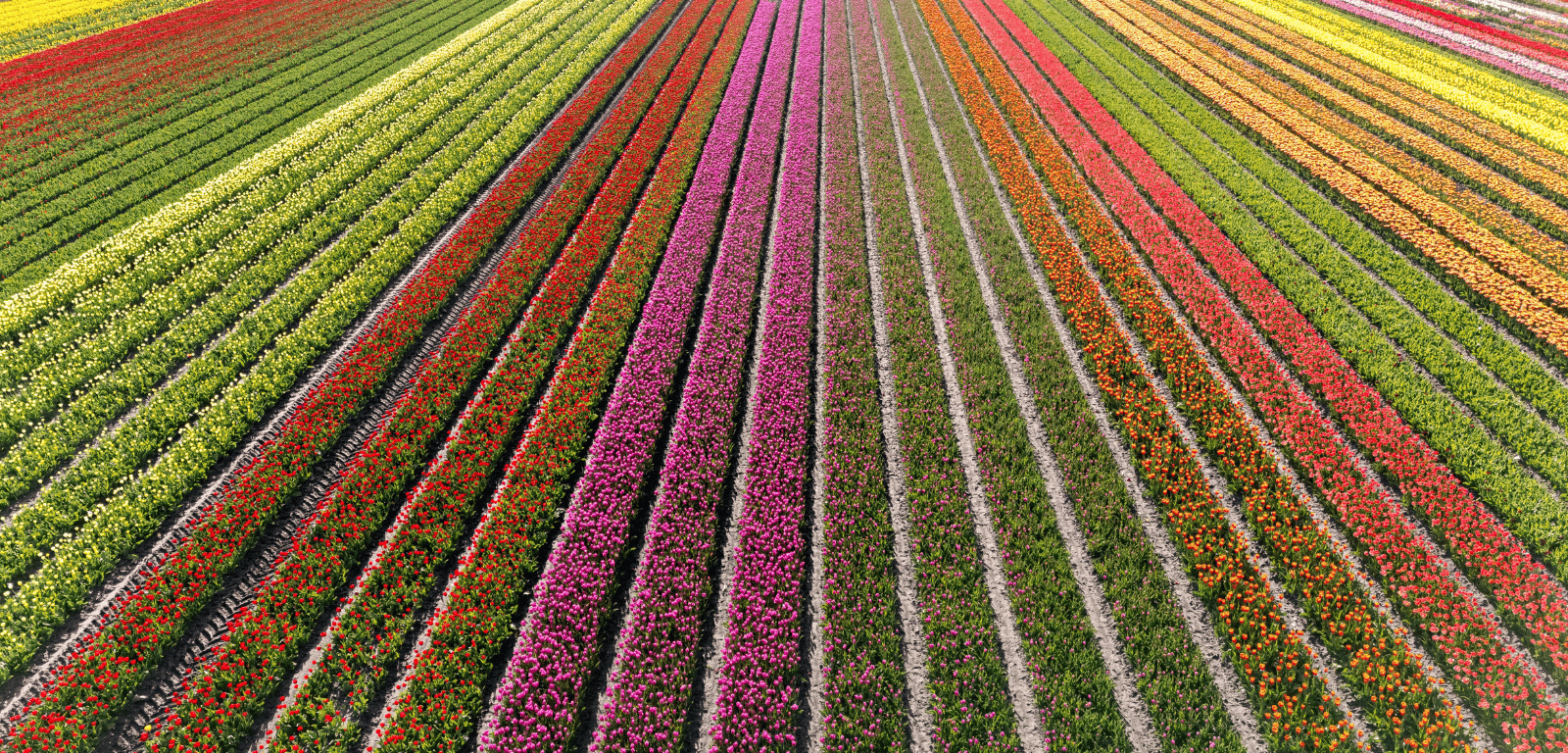
I tappeti sono da tempo un elemento fondamentale dell’arredamento della casa, in quanto apportano calore, stile e carattere a qualsiasi spazio. Ma c’è molto di...