THE 5 MOST FREQUENTLY ASKED QUESTIONS BY PILLOW PRODUCERS
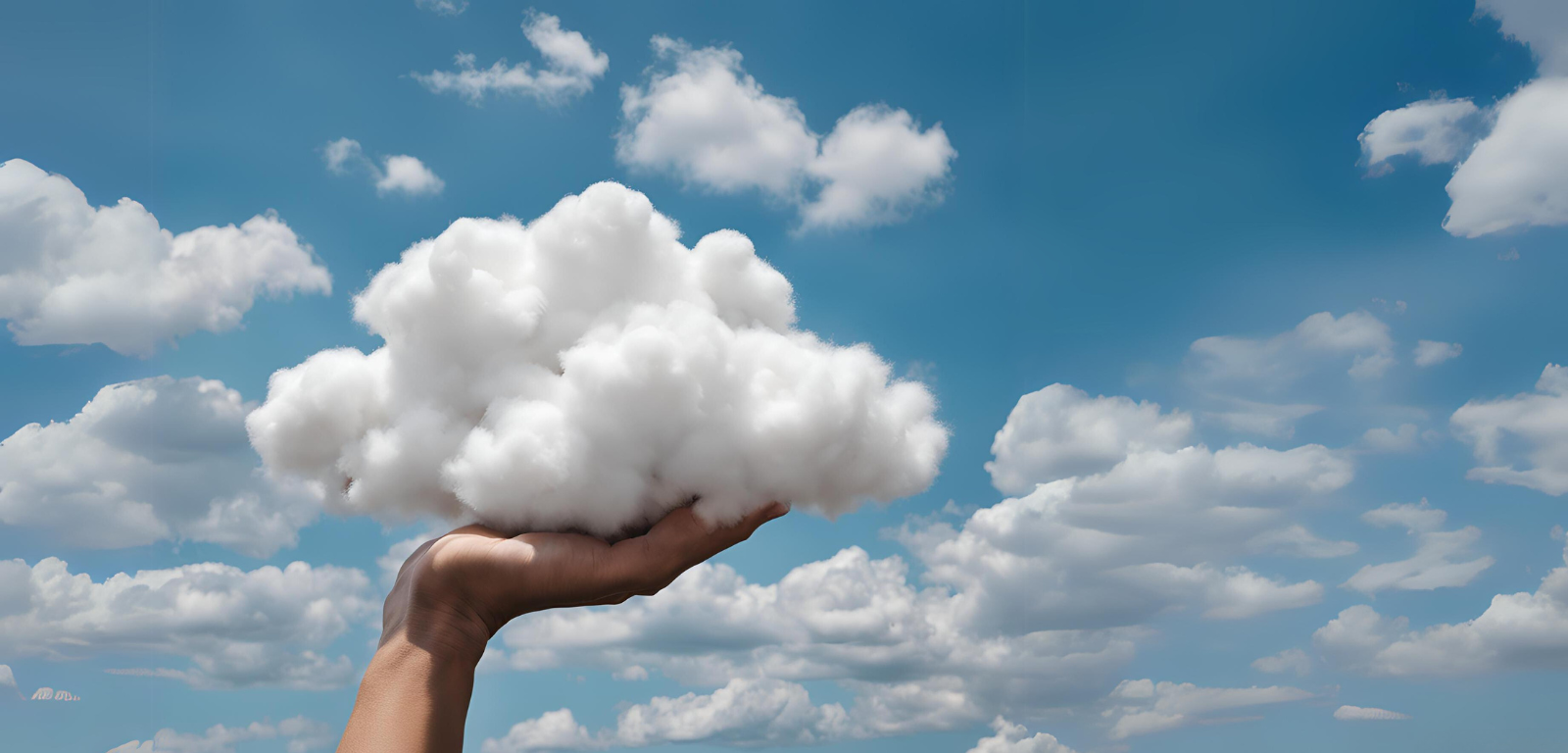
Pillows manufacturers are often faced with several questions that can significantly affect their production process: from filling and packaging material choices to production techniques, we will provide useful information and tips to help them optimize their operations and remain competitive in the market.
1) WHICH FIBER TO USE TO ACHIEVE THE BEST QUALITY PRODUCT?
ANSWER:For those wishing to start making pillows, the fiber’s choice is crucial to ensure quality, comfort, and productivity. The main elements that need to be taken into consideration are:
- Fiber’s type and quality (HCS, Solid, Micro-fiber, Virgin, Recycled or Blended)
- Length (mm) and specific weight (denier, Dtex);
- The result desired in terms of comfort and technique;
- Color;
- Antibacterial and biodegradable properties.
Generally, in the bedding industry, softness, breathability and freshness are sought for the production of pillows. Therefore, the best choice falls on a fairly short fiber or even a microfiber, particularly the 32mm latest generation HCS with a specific weight that goes from 7Dtex to 0.9Dtex.
Regarding sofas, and more generally the upholstered furniture sector, manufacturers’ goal is to ensure a product that supports and also provides a good return. Therefore, longer fibers (> 51 mm) and higher deniers (15Dtex) are used. For increased comfort also the 38mm 1.2Dtex microfiber can be employed.
BRIGHI TIP: For the most demanding sofa manufacturers, 32mm/7Dtex HCS fiber, as well as 38mm/1.2Dtex microfiber, can be also used in the form of balls, which is a filling material that provides excellent “bounce effect” and shape recovery while maintaining the original softness of fiber. This special material can be produced by our BF-300, which is designed to ensure quality production and high performance. Nonetheless, the best performance in resilience and bearing capacity is obtained with blended products, solutions born to guarantee all the benefit of each mixed material. Blends are obtained thanks to our MX-500, where it is possible to dose and mix fiber with various other materials in selected quantities: microfiber, foam scraps, feather and down.
2) WHAT’S THE DIFFERENCE BETWEEN AIR-OPENING TECHNOLOGY AND GENERAL OPENERS?
ANSWER:
Fiber air-opening technology uses a combination of spiked/toothed discs that open fiber with air thrust, without stretching or tensioning the fiber. This method allows the fiber to achieve a greater final volume and a maximum degree of opening, while maintaining its original characteristics such as length and integrity, extending the life of the final product.
The main difference between modern air-opening technologies and general openers lies in the original purpose with which they were created. These latter, in fact, were developed to process fibers for general purposes and uses. However, their frequent and onerous maintenance costs have led to the need to seek specific solutions for certain industries. Therefore, the most enterprising machines’ manufacturers started developing air openers as a specific solution in fiber processing intended for the bedding and, more generally, upholstery industries, where bulkier and less stressed fibers are required. At the same time, they ensure free maintenance.
BRIGHI TIP: Conventional fiber opener machines do not allow increases in capacity over time. In contrast, our OF-550 air fiber opener is a modular machine designed to offer exceptional flexibility in productivity. In particular, with add-on modules, production capacity can be increased significantly (starting at 400 kg/h as standard and rising), enabling manufacturers to quickly optimize operational efficiency.
3) WHAT ARE THE BENEFITS OF “BLOWN” FILLING VERSUS “VACUUM” FILLING?
ANSWER:
“Blown” and “vacuum” technology represent two methods, with different flexibility levels, used for filling products such as pillows, cushions and other items in the world of bedding and upholstered furniture.
Among the main benefits of blown filling there is its extreme versatility in production. Vacuuming machines require breathable covers to work properly, as they must discharge air from the cover. Therefore, if the cover is not breathable, the air will not be discharged and the fiber will not be able to distribute evenly within it. On the other side, blow filling machines allow any type of cover to be accurately filled, including non-breathable ones. This makes them a much more flexible choice suitable for a wider range of applications.
Another significant advantage of blowing machines is that they require about 50% less space than the vacuuming counterpart. The ability to optimize production areas without compromising overall production capacity is an important benefit also combined with a significant increase in machine performance and a reduction of electrical costs.
BRIGHI TIP: Thanks to its innovative software, each of Brighi’s MAC blow filling machines has as its main feature, in addition to high filling accuracy, the ability to manage percentages or grams within desired tolerance ranges. This is because each basket is equipped with a recovery system that, in case of overweight, automatically removes excess material from the basket and returns it to the tower. Such weight correction in contrast is very difficult with vacuum filling technology because once the “weighing” is done, no material can be subtracted.
4) WHAT ELEMENTS SHOULD BE TAKEN INTO CONSIDERATION TO LET FIBER RECOVER QUICKLY WHEN COMPRESSED?
ANSWER:
Even if compression in packaging practices often frightens pillow and cushion manufacturers, tests on fibers, new technologies and accurate studies on processes have demonstrated that the product’s original shape is kept once unpacked. Compression, indeed, is a practice that should be followed more and more, since it leads to space and cost reductions, as the smaller size optimizes storage and transportation expenses. Therefore, to achieve an optimal packaging result, ensuring the quality and the durability of the product, it is good to take into account both the type of fiber and the very characteristics of the machine and sealing bar performing the compression.
Regarding the type of fiber, the most suitable in this case are the hollow ones, since they guarantee a greater return than solid fibers. This is especially true if the goal is to flat pack voluminous pillows, cushions or quilts, which require a quick return to their original shape. When dealing with resilience and quick return, we do not consider only virgin fibers but also recycled ones.
The importance of a well-processed fiber goes hand in hand with a machine that performs accurate and safe compression. In particular, the machine should take into account the fiber and allow the compression to be adjusted according to it.
BRIGHI TIP: All of our compression technologies, from fully automatic (EB-500) to semi-automatic (EB-400 and LF-100), ensure compression adjustments according to the desired result, up to a maximum level of 100%, thanks to double sealing bars that ensure that there is no air channel left. These adjustments can be saved in the recipes depending on the fiber utilized.
5) WHAT IS THE RIGHT BAG TO KEEP FLAT PACK FOR THE LONGEST TIME?
ANSWER:
The durability of flat packaging depends on three main factors:
- the composition of the plastic and its number of barrier layers
- the value of OTR, or oxygen transmission rate
- the type of sealing bar
Plastic can be multilayered, meaning it can have several protective barriers essential for preserving the quality and safety of products. By combining different materials in the multilayer structure, OTR levels can be considerably reduced. In the case of products such as pillows and cushions, the packaging consists of an inner barrier layer, glue, and two outer polyethylene layers. Without the inner layer, the porous nature of polyethylene would not allow the packaging to remain flat for very long.
The last crucial element in this process is the sealing bar. It must ensure uniform pressure and heat distribution to avoid uneven sealing that could compromise the integrity of the packaging or deform the pillow contained within.
If all elements are adhered to and the processes in creating the packaging are done correctly and with proper care, it is possible for the flat packaging to remain intact for a year and a half (18 months).
BRIGHI TIP: The EB-500 is our most automated solution for flat packaging. In addition to traditional sealing, the machine disposes of a second sealing bar that serves as a back-up for maximum seal security for different thicknesses. This double sealing feature is available also for the semi-automatic version (EB-400) and for the roll packing one (ER-500), and allows to seal up until 150 microns.
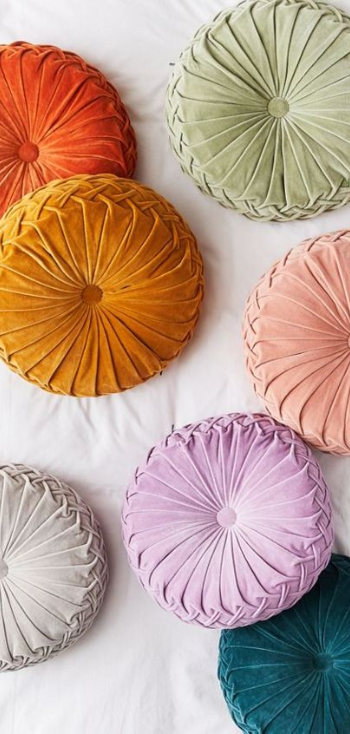