CLOSING THE LOOP: THE RECYCLING POTENTIAL IN HOME TEXTILE
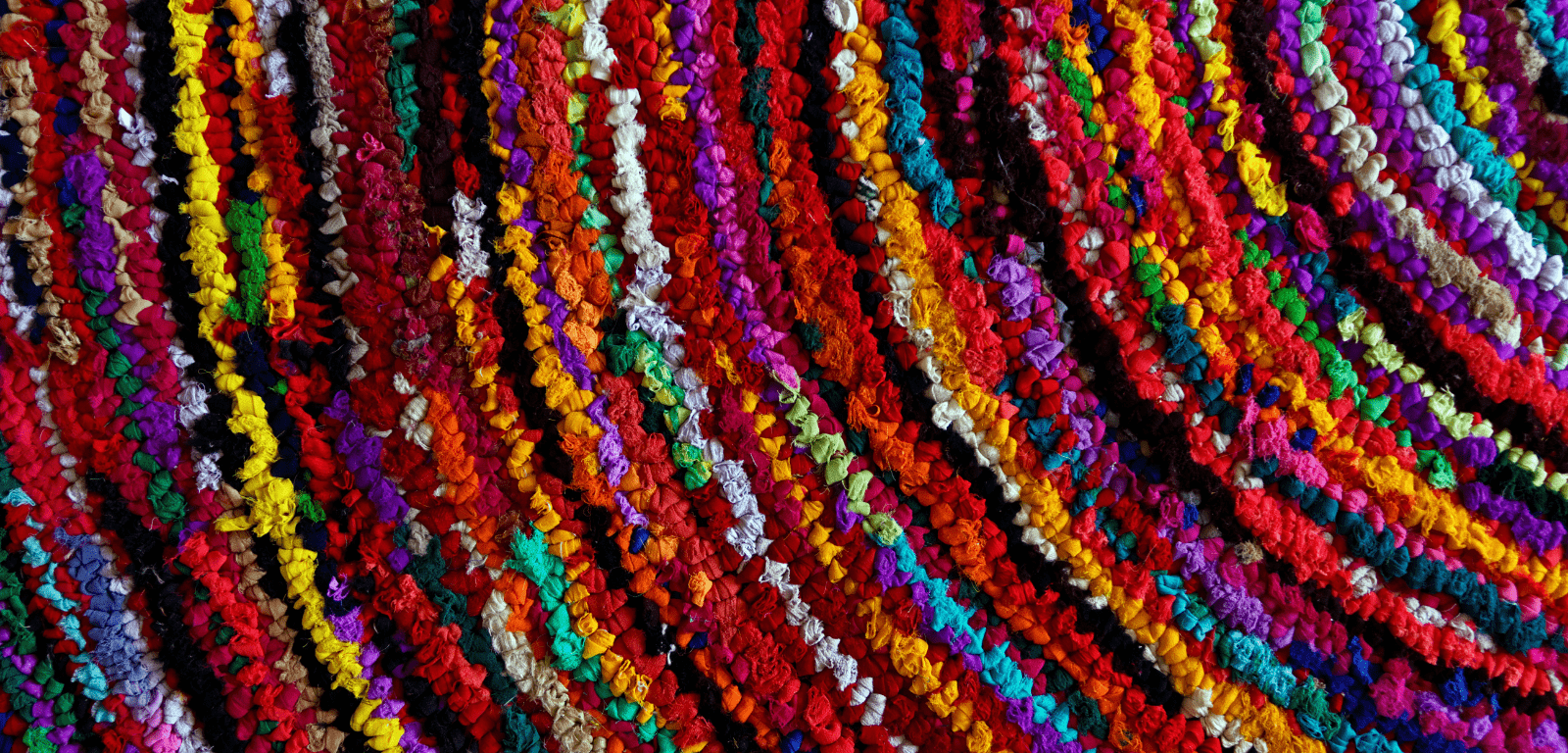
The textile industry is rapidly expanding, with fibers and fabrics being predominantly used in clothing and home textiles. This surge in production has led to an urgent need to manage vast amounts of waste—amounting to an average of 15 kg yearly per person in Europe alone. To put this into perspective, textiles rank as the 4th largest sector in terms of raw material and water consumption, trailing only food, construction, and transport, according to the European Commission’s Circular Economy Action Plan.
As might be expected, 85% of this waste comes from post-consumer, i.e., used and discarded textiles. The remainder belongs to the post-industrial category, meaning the surplus fabric produced during garment manufacturing, and pre-consumer, i.e., failed products and unsold merchandise.
FIBER AND FABRICS RECYCLING TECHNOLOGIES
Despite of the textile waste typology, research is underway to develop methods for reintegrating textile waste back into the production cycle and “close the loop”. Recycling methods for fiber and fabrics are divided into two macro categories: mechanical recycling and chemical recycling.
MECHANICAL RECYCLING
This is one of the simplest and most cost-effective recycling methods for post-industrial waste, and it is currently the most widely used. The process relies on mechanical actions like cutting, tearing, and shredding to transform textiles back into usable fibers. These resulting fibers can either be directly utilized to produce wipes, padding, non-woven products, or acoustic and thermal insulation materials, or they can undergo limited rounds of spinning for reuse. This latter is known as fiber-to-fiber recycling, and it is gaining significant relevance due to its upcycling potential.
CHEMICAL RECYCLING
This technique involves breaking down the polymer structure of textile fibers, reducing textiles to their basic components (depolymerization) and then repolymerizes them, producing a high-quality end product similar to virgin fibers. This process supports upcycling, as it creates fibers that can be used for higher-quality fabric products. However, these methods are generally more challenging to manage and not always economically viable.
Despite the potential of such technologies, there are basic barriers that lie in the fiber composition and the fabric construction. In the first instance, the difficulty arises from recycling materials that are not composed entirely of the same fiber, which requires more careful sorting, and still result in a lower quality final material. The pre-processing phase becomes even more complicated with fabrics, as they may be part of products that include zippers, buttons, and other hard components that must be meticulously removed to facilitate processing. Additionally, woven fabrics are generally more complex to recycle than knits due to their rigid and sturdy structure, which makes the separation of internal fibers more labor-intensive.
HOME TEXTILE RECYCLING SOLUTIONS
According to the McKinsey study “Scaling textile recycling in Europe—turning waste into value,” if current barriers were overcome through increased investment in textile recycling technologies, these latter could reach their full potential, and the proportion of recyclable textile waste could rise from 18% to 26% within 10 years. Additionally, many companies could finally achieve a greener footprint and reap the associated benefits.
Some companies have already made textile waste recycling their core business, giving discarded materials new life with similar or even improved quality. In the home textile industry, for instance, recycled fibers can be reintroduced into the production cycle as pillow covers (especially in non-woven fabrics) or as filling materials.
Additionally, fabrics from defective or unsold products present significant opportunities, as they do not require the same treatments as post-consumer items and can be reprocessed into higher-quality products. One of the most striking examples is quilted fabric, which, due to its simple construction and thickness allows for a variety of recycling and reusing options. It can be repurposed to make new quilts, pet beds, bags, decorative cushions’ cases or more generally bed linens. Moreover, if processed adding also virgin fiber, it can produce upcycled products.
In this sector, not only can textile scraps be repurposed, but mattresses also offer significant opportunities. It’s worth noting that each year, 5 million mattresses are discarded in landfills in Italy alone, with each occupying up to 40 ft3 of space (more than 1m3). In reality, each mattress is made up of components that can be recovered (75%) and reused in other industries once processed (such as the production of insulation for the construction, civil, and steel sectors). For instance, foam can be shredded and rebonded to create new products such as carpets, carpet padding, or even new mattresses, and in some cases, it can be processed into insulation materials.
WHAT BRIGHI BRINGS ON THE TABLEAt Brighi Group, we strongly believe that transitioning to a circular and sustainable business model is only possible with the right technology. Recycling production waste before it is used—thus minimizing the need for more complex processing—is a top priority. Our commitment is to equip companies with the machinery they need to efficiently recycle their own waste, enabling them to become self-sufficient in the process. By implementing advanced recycling methods and technologies for production waste, companies will not only be relieved of the burden of disposing of their waste and its associated costs, but also transform their production cycle into one that is both environmentally sustainable and economically profitable.
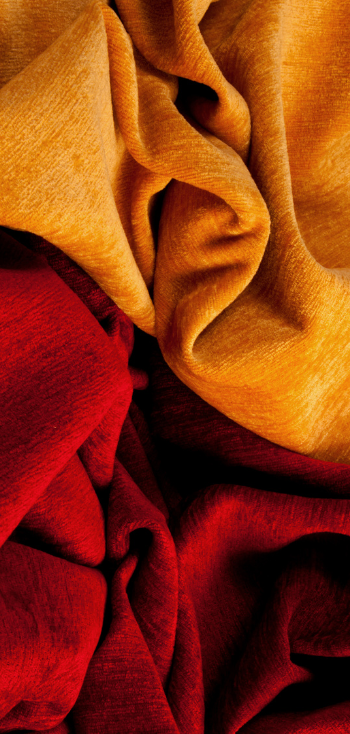